Reference projects
Here you can find a growing presentation of research results from the field of Car Body Shop 4.0.

Whether in large-scale production, in which switching is carried out between several models, or in prototype and small-scale production: Each work step previously required elaborately planned and expensively manufactured, model-specific fixtures for joining, measuring and depositing. In the process, the support or clamping points must be changed spatially in various degrees of freedom in the range of a few to a few hundred millimeters.
- • Resource efficiency increase by reducing the number of different model-specific fixtures
- • Productivity increase due to fewer fixture changes
- • Changeover in the production cycle and in the wild mix (free sequence of assemblies to be produced)
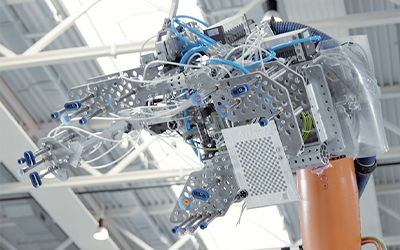
Not only the joining devices themselves, but also all the necessary operating equipment for the upstream and downstream process steps must be able to ensure adaptive, safe and robust component feeding. In addition, these handling systems are predominantly robot-guided and thus subject to high dynamic loads. A large variety of components represents a further enormous challenge in the flexibilization (adaptive adjustment) of car body assembly stations. Various grippers, which are adapted to the respective processes, have been developed to ensure safe component transport in the wild mix from the load carriers into the production device.
- • Increase in resource efficiency due to reduction in the number of different model-specific grippers
- • Productivity increase due to fewer tool changes on the robot (docking)
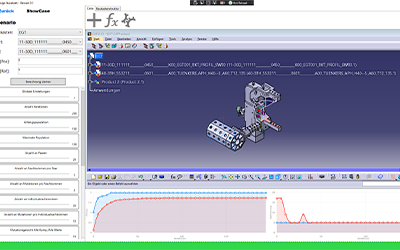
The Design Assistant (DesignAssistant) is an innovative software for automating and optimizing design processes for modular-based operating equipment, such as grippers in car body construction.
- • mathematical optimization methods for generating design proposals guarantee significantly faster gripper design (> 50% time savings)
- • designer retains full control and can intervene in the decision-making process
- • uniform methodical procedure ensures conformity of design processes with guidelines
- • in-house know-how is retained and can be transferred more quickly to new employees
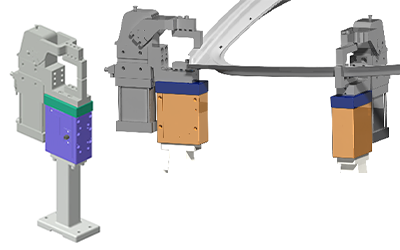
The mechanical readjustment of fixtures for the temporary fixing of two or more components to influence geometric tolerances of the joined assembly is called "shimming". Even in large series, this adjustment in the range of 0.1 to 10 mm is still carried out manually using shim plates and therefore requires a system shutdown. In order to enable this adjustment in the series cycle, actuators were developed that have the required accuracy on the one hand and the necessary rigidity on the other. A positive side effect is that documentation can now be fully automated and the handwritten shim book on the body shop line is no longer necessary.
- • Shimming in series cycle
- • size and stiffness comparable to conventional consoles
- • automatic documentation of adjustment parameters
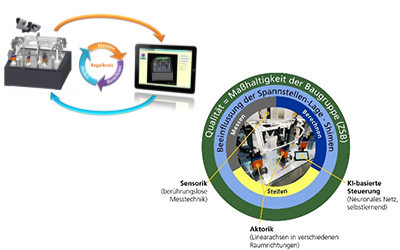
"Adjustment at the touch of a button“
By using a mathematical model, the experience-based adjustment processes are reproduced, i.e. learned by means of an artificial neural network. The training is performed by linking measurement data and resulting changes to the contour pieces by "shimming". The AI-based software correlates the quality data with the fixture's adjustment settings. After a learning phase of the AI, the software ("adjustment wizard") independently generates suitable adjustment parameters based on measurement data of the individual parts or the joined assembly. In the future, the system will thus be able to react autonomously to quality fluctuations of the input components and carry out the necessary adjustment measures within the production cycle.
- • shortening of the plant start-up time
- • Reproducible adjustment in the production cycle
- • Adjustment without entering the plant protection circuit
- • Shortening of the entire control cycle
- • Increase in production
- • Reduction of rework and scrap
- • Automatic documentation of adjustment parameters
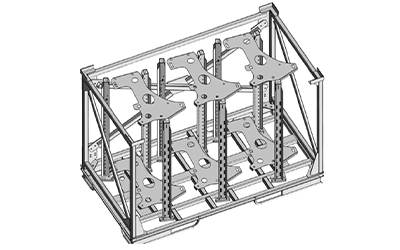
The automatic planning assistant is an innovative PC software that can be used to optimize planning and design processes for the development and production of containers and special load carriers.
- • automatic generation of the CAD-based container design enables an efficiency increase of up to 75 percent compared to conventional engineering processes
- • integrated automatic component and installation space analysis optimizes component arrangement and number per container (up to 12 percent better space utilization)
- • uniform methodical approach ensures conformity of design processes with guidelines
- • in-house know-how is retained and can be transferred more quickly to new employees
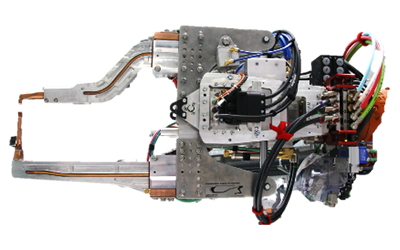
Lightweight construction is a basic requirement for the development of moving equipment, especially for robot-guided tools, in order to make processes dynamic and energy-efficient. Particularly in vehicle body-in-white construction, spot-welding guns have a high application density and offer great potential for optimization.
- • weight reduction of the tong base body by 45%
- • reduction of overall width by 50%
- • Reduction of the number of variants due to symmetrical design
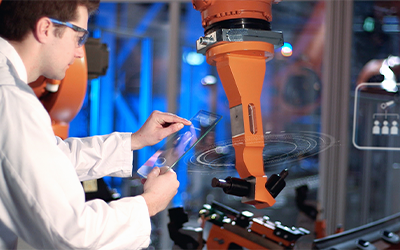
As a result of their great flexibility and the associated wide range of possible applications, 6-axis robots are particularly suitable for an agile production environment. In contrast, they have a lower stiffness in the various axes and joints compared to machine tools, which can lead to position inaccuracies, especially in the course of the process with changing loads. For this reason, a methodology was developed to compensate for this displacement, which can correct the position during the running process based on a force measurement directly on the robot tool.
- • Quality increase in the robot-guided manufacturing process
- • Increase in productivity due to reduced programming efforts
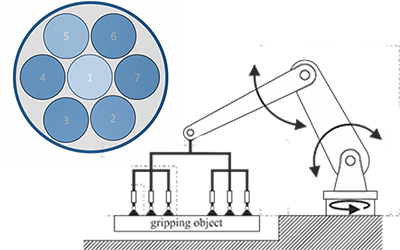
This innovative handling system uses the advantages of vacuum technology without relying on a compressed air supply. For this purpose, an octopus was modeled after a bionic model. The actuation of the suction cups is realized by the use of artificial muscles. Individual groups of suction cups, so-called clusters, act in a self-organizing manner and are controlled with the aid of artificial intelligence. Reinforcement learning is used in this process. The system is trained with linear regression models and decides itself whether to re-suckle in the event of pressure losses
- • Vision „Compressed Air-Free Body Shop“
- • Elimination of compressed air supply
- • Reduction of energy consumption by 16%
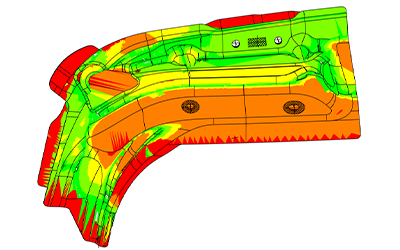
With the help of the Geometry Comparison software tool, the differences between two component positions can be calculated and graphically visualized. Triangulated models of the corresponding component data serve as a basis.
- • Automatic comparison of very large data sets (batch operation)
- • automated export function documents the results
- • Collision comparison between the modified part geometries (contours, features) and the respective part-specific fixtures represents possible adjustments
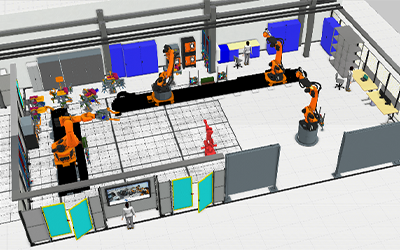
By the end of 2021, a modular robot system will be converted and set up, which will offer the possibility of carrying out research tasks for a wide range of industrial applications (automotive construction, aircraft construction, machine tool construction) and in different areas of application (structural design, body construction, final assembly), while always using the latest control technology (incl. edge computing, OPC-UA, MQTT, TSN, etc.).
- • Multi-robot system
- • Modularly configurable
- • Integration of different production processes (forming, joining, machining)
- • Virtual production twin for faster IBN, scenario analysis and inline monitoring